Printing processes are crucial as they define the design's final look. Knowing them helps designers pick the right method, ensuring accurate color and detail reproduction and preventing product errors. It also optimizes cost, time, and communication, being essential for design skills. This article will cover the principles, processes, features, and uses of various printing techniques.
Printing processes are of great importance as they determine the actual presentation effect of the design. Familiarity with the processes can assist designers in choosing the appropriate printing methods, ensuring accurate presentation of colors and details and avoiding deviations in the finished products. Meanwhile, understanding the processes can also optimize costs and production time and improve communication efficiency, which is the key to design professional capabilities.
This article will detail the principles, processes, characteristics, and applications of screen printing, gravure printing, UV printing, offset printing, digital printing, heat transfer printing, and foil stamping/gold/silver stamping processes.
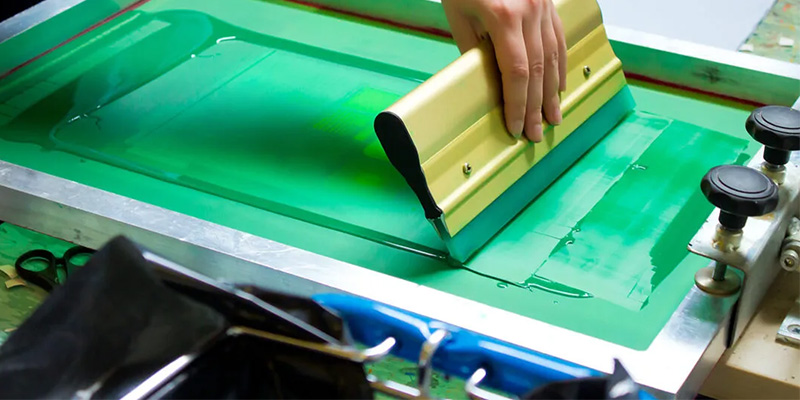
1. Screen Printing
Basic Principle and Technological Process
Screen printing is a kind of stencil printing technology. Its basic principle is to use a silk screen as the plate base and make a silk screen printing plate with graphics and text through the photosensitive plate-making method. During the printing process, under the squeezing of the squeegee, the ink is transferred to the substrate through the mesh holes of the graphic and text parts, forming the same graphics and text as the original manuscript.
The technological process can be roughly divided into the following steps:
- Prepare the screen frame and photosensitive film. Clean the screen frame and remove oil stains.
- Exposure. Press the photosensitive film and the base plate tightly in the plate-making machine and expose them with a light source.
- Development. Soak the screen film with warm water and spray it with a water nozzle to remove the non-photosensitive parts.
- Film pasting. Paste the film surface of the film after exposure and development onto the silk screen, ensuring that the film is firmly in contact with the screen.
- Drying. Place the silk screen with the pasted film in an oven and dry it for printing.
Application Fields and Characteristics
The application fields of screen printing are very extensive, including but not limited to the following industries:
- Glass packaging industry: It is used for printing words or patterns on glass container products.
- Plastic packaging industry: It is used for packaging printing of plastic films to protect items from external influences.
- Metal packaging industry: It is used for packaging printing of metal containers, which requires strong ink adhesion and abrasion resistance.
- Paper packaging industry: It is used for printing patterns on paper to improve the grade of product packaging.
- Ceramic packaging industry: It is used for printing patterns on ceramic products to increase their aesthetic appeal.
The characteristics of screen printing include:
- Strong adaptability:
It can print on flat surfaces, curved surfaces, spherical surfaces, and concave and convex surfaces.
- Thick ink layer:
The ink layer thickness of screen printing can generally reach 30μm, with a strong three-dimensional effect.
- Vivid colors:
Various inks and coatings can be used, and it has strong color expression ability.
- Strong light resistance:
It is suitable for printing products such as outdoor advertisements and signs that are exposed to sunlight for a long time.
- Flexible printing format:
It can carry out large-area or ultra-small, ultra-high-precision printing of special items.
- Simple operation:
The equipment is simple and the operation is convenient, which is suitable for individual handicraft production and mechanized production.
Due to its unique advantages, screen printing is known as the "King of Decoration Printing" in decoration printing. It is applicable to the printing of various materials and is one of the printing methods with a wide range of applications.
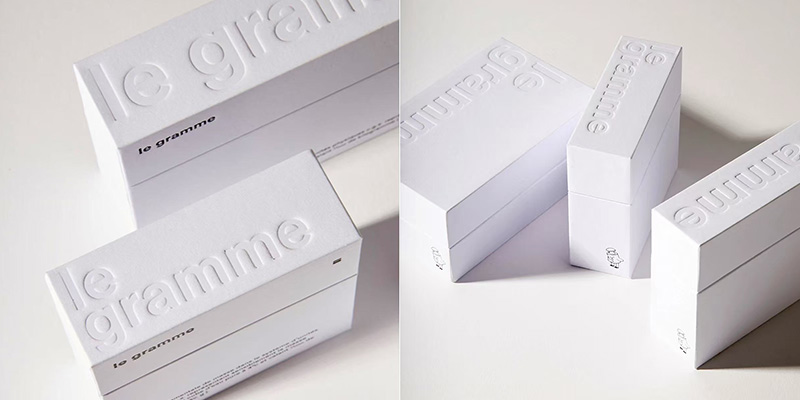
2. Gravure Printing
Printing Principle and Characteristics
Gravure printing is a direct printing method. Its core principle is to utilize the recessed graphic and text parts on the gravure plate to store ink and transfer the ink onto the substrate through the pressure of the printing press, forming clear patterns and texts.
Printing Principle:
The printing plate of gravure printing is crucial. The graphic and text parts are lower than the non-graphic and text parts, forming recessed imprints. The ink is filled into these recessed imprints, while the non-graphic and text parts remain clean. During the printing process, the pressure of the printing press enables the ink in the recesses to be transferred onto the substrate, forming the required graphics and texts.
Characteristics:
- Thick Ink Layer:
The ink layer thickness of gravure printing is usually thicker than that of other printing methods and can reach more than 20μm, making the colors of printed products more vivid and three-dimensional.
- Vivid Colors:
Thanks to the thick ink layer, gravure printing can achieve high-saturation color effects and is suitable for printing high-quality color images.
- High Printing Durability:
The printing plate of gravure printing has strong durability and can withstand millions of printings, which is suitable for mass production.
- Wide Range of Application:
Gravure printing is applicable to a variety of substrates, including paper, plastic films, metal foils, etc., and can meet the printing requirements of different products.
- Continuous Printing:
The gravure printing machine can conduct high-speed continuous printing and is suitable for the production of long-run printed products.
- Good Anti-counterfeiting Performance:
Gravure printing is often used for the printing of valuable securities, anti-counterfeiting labels and other products because its printed patterns are difficult to replicate.
Application Range
Due to its unique advantages, gravure printing is widely used in multiple fields:
- Packaging Printing:
Gravure printing is widely used in the packaging industry, especially in the printing of plastic flexible packaging, paper boxes, labels and other products, and can provide high-quality printing effects.
- Publishing Printing:
In Europe and America, gravure printing is often used for the production of mass-printed products such as newspapers and direct mail advertisements.
- Printing of Valuable Securities:
Gravure printing is suitable for the printing of valuable securities such as currencies, stamps and securities because of its good anti-counterfeiting performance.
- Decorative Printing:
On decorative materials, such as wallpapers and decorative materials, gravure printing can print continuous patterns and increase the aesthetics of products.
- Industrial Printing:
In the industrial field, gravure printing is used for printing circuit boards, decorative films of electronic products, etc., and is favored because of its fine lines and thick ink layer.
The characteristics of high printing durability and vivid colors of gravure printing give it a significant cost advantage in long-run printing. Although its plate-making cost is relatively high, the unit printing cost is low for mass production, so it occupies an important position in the market.
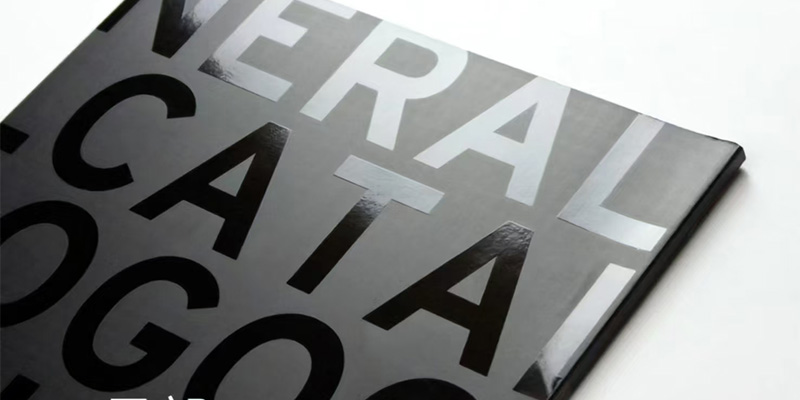
3. UV Printing
UV Ink and Curing Technology
The core of UV printing technology lies in UV ink and the curing process. UV ink is a special formulated ink, and its key components can quickly cure to form a film under ultraviolet irradiation.
Composition of UV Ink:
- Prepolymer: As the main component of the ink, it usually accounts for 50 - 70% of the total ink amount.
- Monomer: Serving as an active diluent, it adjusts the viscosity of the ink and improves its printing performance.
- Photoinitiator: It generates free radicals under ultraviolet irradiation and initiates the polymerization reaction of the prepolymer and the monomer.
- Pigment: It provides the color of the ink and can be either organic or inorganic pigments.
Curing Process:
UV curing is a photochemical reaction. Liquid UV ink cures rapidly under ultraviolet irradiation. The curing speed is affected by multiple factors, including the intensity and wavelength of the UV light source, the thickness of the ink layer, and the light transmittance of the substrate material. The power density of the UV lamp is crucial to the curing effect, and the commonly used specifications generally range from 40W/cm to 2000W/cm.
Curing Equipment:
- UV Lamp Types:
They include mercury lamps and LED cold light source lamps. The latter has gradually become the mainstream due to its advantages of low energy consumption, long service life, and quick start-up.
- Heat Dissipation Methods:
There are fan-type and water-cooling type. The former is simple to maintain but may cause thermal deformation of the printing materials, while the latter has good heat dissipation effect but is complicated to maintain.
Advantages and Limitations
UV printing technology has obvious advantages in the modern printing industry, but it also has some limitations.
Advantages:
- Rapid Curing: UV ink cures instantly under ultraviolet irradiation, significantly improving production efficiency.
- Environmental Protection: UV ink does not contain volatile organic compounds (VOCs), which is friendly to the environment.
- Wide Applicability: UV printing is applicable to a variety of substrate materials, including non-absorbent and absorbent materials.
- High Gloss: The ink layer after UV curing has high gloss and characteristics of abrasion resistance and corrosion resistance.
- Space Saving: There is no need for powder spraying and long-time drying in traditional printing, saving the post-printing processing space.
Limitations:
- Cost: The costs of UV ink and curing equipment are relatively high, increasing the production cost.
- Technical Requirements: There are specific requirements for the temperature and humidity of the operating environment, which need to be precisely controlled to ensure printing quality.
- Ink Adhesion: UV ink may generate relatively large internal stress during the curing process, affecting the adhesion of the ink to the substrate material.
- Equipment Maintenance: UV light tubes have a limited service life and need to be replaced regularly, and the maintenance cost is high.
- Color Performance: On some materials, the color saturation of UV printing may be inferior to that of traditional ink.
In conclusion, UV printing technology demonstrates strong market competitiveness in fields such as packaging printing and high-end commercial printing due to its characteristics of rapid curing, environmental protection, and high gloss. However, its relatively high costs and technical requirements limit its popularity in some application scenarios. With the continuous progress of technology, it is expected that UV printing will occupy a more important position in the future printing industry.
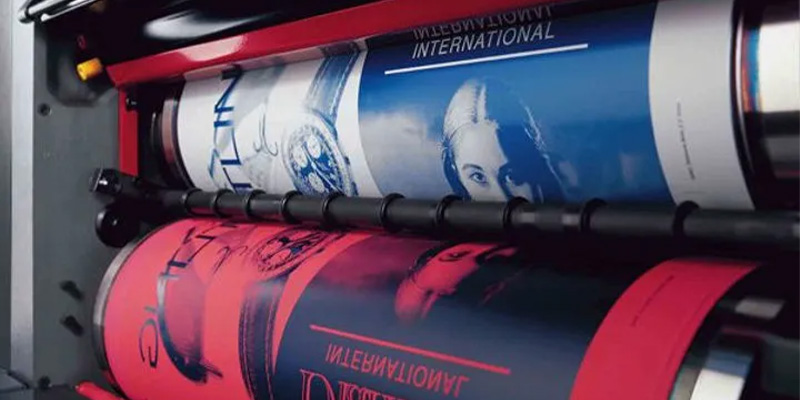
4. Offset Printing
Indirect Printing Principle
Offset printing, also known as lithographic printing, is a widely used indirect printing technique. Its core principle is based on the mutual repulsion property of ink and water. Through the interaction between the graphic and text parts and the non-graphic and text parts, the transfer of printed graphics and texts is achieved.
Printing Principle:
The printing plate of offset printing is flat. The graphic and text parts and the blank parts are on the same plane, but they have different surface energies. The graphic and text parts are oleophilic and hydrophobic, while the blank parts are hydrophilic and oleophobic. During the printing process, first, the dampening roller applies dampening solution to the hydrophilic non-graphic and text parts of the plate cylinder. Then, multiple ink transfer rollers apply ink to the oleophilic (ink-receptive) graphic and text parts of the plate cylinder. The ink and the dampening solution form a stable distribution on the printing plate. Subsequently, the ink is transferred from the plate cylinder to the blanket cylinder and then, under the action of the impression cylinder, is transferred from the blanket cylinder to the substrate to form the printed product.
Characteristics:
- Offset printing is an indirect printing method. The ink is first transferred to the blanket and then to paper or other substrates.
- Offset printing can achieve high-quality printing effects with clear graphics and texts and vivid colors, and it is suitable for mass production.
- Offset printing presses can handle a variety of substrates, such as paper, plastic, metal, etc., having a wide range of applicability.
- Offset printing adopts the ink-water balance technique. By precisely controlling the amounts of ink and dampening solution, the printing quality is ensured.
Quality Control and Application
The quality control of offset printing is a key link in ensuring printing quality, involving multiple aspects such as printing pressure, ink-water balance, and overprinting accuracy.
Quality Control:
- Printing Pressure:
Appropriate printing pressure ensures the even transfer of ink and avoids blurred prints or paper damage caused by excessive pressure.
- Ink-Water Balance:
Precisely control the pH value and the amount of the dampening solution to ensure the stable transfer of ink and the cleanliness of the printing plate.
- Overprinting Accuracy:
Through precise equipment adjustment and monitoring, ensure that the overprinting of each color plate is accurate in multi-color printing and avoid color distortion.
- Color Management:
Use a color control system to ensure the consistency and accuracy of printing colors and meet the high standards of customers.
- Printing Materials:
Select appropriate paper and ink. Different papers' ink absorption and surface characteristics will affect the printing effect.
Application Fields:
- Packaging Printing:
Offset printing is widely used in the packaging industry, such as in food packaging, cosmetic packaging, and pharmaceutical packaging, providing beautiful visual effects and good printing quality.
- Publishing Printing:
For the printing of publications like books, magazines, and newspapers, offset printing can meet the mass production requirements with high quality.
- Commercial Printing:
For commercial printed products like business cards, letter paper, and envelopes, offset printing provides stable and efficient printing services.
- Advertising Printing:
For billboards, posters, brochures, etc., offset printing can achieve high-definition and vivid color printing effects to attract the attention of the target audience.
Offset printing technology occupies an important position in the printing industry due to its high efficiency, high quality, and wide applicability. Through strict quality control and continuous technological innovation, offset printing will continue to play a key role in various printing applications.
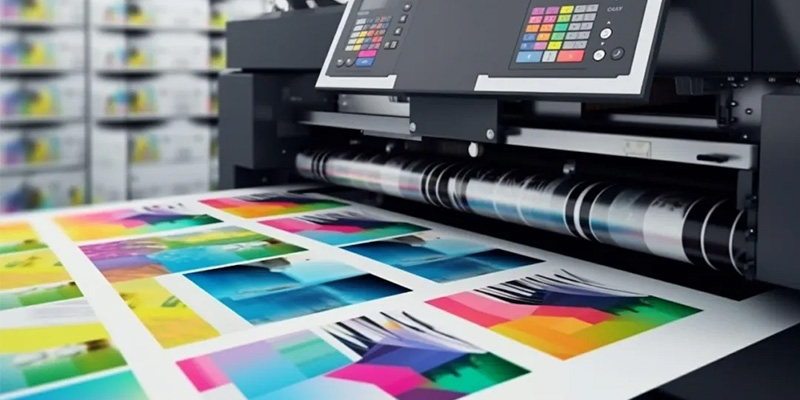
5. Digital Printing
Digital Printing Technology and Features
Digital printing is a production method that uses digital technology for printing. It directly controls the printing machine through digital files without the need for plate-making, enabling fast and flexible printing services.
Technical Features:
- Direct Printing from Digital Files:
Digital printing does not require the traditional plate-making process. Digital files are directly transmitted to the printing equipment to achieve rapid printing.
- Variable Data Printing:
Each printed product can be different, which is suitable for personalized printing needs, such as variable barcodes, personalized images, etc.
- Instant Printing:
Digital printing machines can instantly adjust printing parameters to adapt to different order requirements and shorten the production cycle.
- Cost-Effectiveness of Small-Batch Printing:
Since there is no need for large-scale plate-making, the cost of small-batch printing is relatively low, making it suitable for on-demand printing.
- Color Management:
Digital printing machines are equipped with high-precision color management systems to ensure the consistency and accuracy of colors.
- Environmental Protection:
The digital printing process does not require the use of chemical agents, producing fewer waste products and wastewater, and having a low impact on the environment.
Technical Advantages:
- Quick Response:
Digital printing can quickly adjust printing parameters to adapt to urgent orders and rapidly changing market demands.
- Personalized Services:
It meets personalized printing needs and provides customized services for customers, increasing the added value of products.
- Flexible Printing Options:
Digital printing can easily handle various file formats, support multiple substrates, and provide diverse printing options.
- Cost-Effectiveness:
The cost-effectiveness of small-batch printing and on-demand printing is high, which is suitable for short-run printing and testing market reactions.
- Color Consistency:
The color management system of digital printing machines ensures the consistency of colors in each printing, meeting the high-quality requirements of printing.
Personalized Printing Applications
Personalized printing is an important application area of digital printing technology. It meets the market's demand for personalized products and provides customized printing services for customers.
Application Areas:
- Personalized Gifts:
Such as customized T-shirts, cups, photo albums, greeting cards, etc. Consumers can design patterns and texts according to their own preferences.
- Business Promotional Materials:
Personalized brochures, business cards, posters, etc. help enterprises enhance their brand image and market competitiveness.
- Packaging Printing:
Personalized packaging can enhance the uniqueness and recognition of products and attract consumers' attention.
- Publications:
Such as personalized books, magazines, annual reports, etc., providing customized publishing services.
- Labels and Tags:
Personalized labels and tags can be used for product identification, brand promotion, etc.
Market Trends:
- Growth in Consumer Demand:
As consumers' demand for personalized products increases, the personalized printing market will continue to grow.
- Technological Progress:
Advances in digital printing technology, such as increased printing speed and reduced costs, will further promote the development of the personalized printing market.
- Increased Environmental Awareness:
Environmentally friendly digital printing technology will be more popular because it reduces environmental pollution in the printing process.
- Online Printing Services:
The rise of online printing platforms has made personalized printing services more convenient and accessible.
The development of digital printing technology provides strong support for personalized printing, making printing services more flexible, efficient, and environmentally friendly. With the growth of market demand and continuous technological progress, personalized printing will play an increasingly important role in the future printing industry.
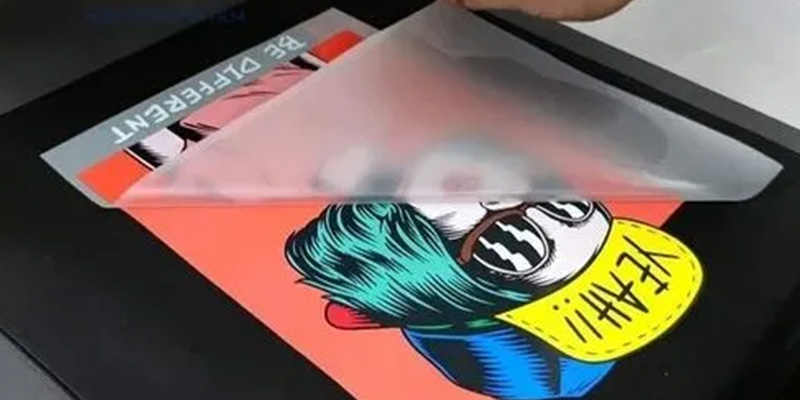
6. Heat Transfer Printing
Transfer Process and Materials
Heat transfer printing is a printing technique that transfers patterns or texts onto the surface of a substrate through heat and pressure. The core of this technique lies in heat transfer ink and special transfer paper or film.
Transfer Process:
- Sublimation Heat Transfer:
Utilize sublimation ink to print on special paper, and then transfer the dyes in the ink into the substrate through high temperature and high pressure to form a penetration effect.
- Heat Transfer Decal:
Print patterns on PET sheets and coat hot melt adhesive on the back. Then, transfer the patterns and the adhesive layer onto the substrate through heat pressing to form an image attached to the surface.
Materials:
- Transfer Paper/Film:
Special transfer paper or film coated with heat transfer ink is the key material in the transfer process.
- Heat Transfer Ink:
It contains dyes or pigments that can be sublimated, as well as binders and additives, and is used for printing on transfer paper.
- Hot Melt Adhesive:
It is used for heat transfer decal to firmly adhere the patterns to the substrate.
Technological Process:
- Design patterns and make them into transfer paper or film.
- Adjust the heat transfer equipment to an appropriate temperature and pressure.
- Align the transfer paper or film with the substrate and put them into the heat transfer equipment.
- Heat and press to transfer the dyes in the ink into the substrate or make the hot melt adhesive adhere the patterns to the substrate.
- Take out the transferred product after cooling to complete the transfer.
Characteristics:
- Wide Applicability: It is applicable to a variety of materials, such as plastics, metals, ceramics, fabrics, etc.
- Vivid Colors: The patterns after transfer have full colors and high color reproduction.
- Strong Durability: The patterns after heat transfer have good resistance to washing and friction.
- Simple Operation: It is suitable for small-batch production and personalized customization.
Application Fields
Heat transfer printing technology has been widely used in many industries due to its unique advantages.
- Garment Industry: Transfer personalized patterns and texts onto clothing such as T-shirts, hats, shoes, etc. to meet personalized needs.
- Home Decoration: Transfer patterns onto household items such as cups, plates, ceramic tiles, etc. to increase the aesthetics and personalization of products.
- Promotional Gifts: Make personalized promotional gifts, such as pens and notebooks printed with company logos, to enhance the corporate image.
- Electronic Products: Transfer decorative patterns onto electronic products such as mobile phone cases and computer casings to enhance the attractiveness of products.
- Outdoor Advertising: Transfer advertising content onto billboards and banners to improve the visual effect of advertisements.
- Industrial Manufacturing: Transfer logos, warning labels, etc. onto various industrial products to improve the identification and safety of products.
- Anti-counterfeiting Labels: Make anti-counterfeiting labels and holograms for product anti-counterfeiting and brand protection.
Heat transfer printing technology plays an increasingly important role in the modern printing industry with its flexible customization ability and wide applicability. With the progress of technology and the development of the market, the application fields of heat transfer printing will be further expanded.
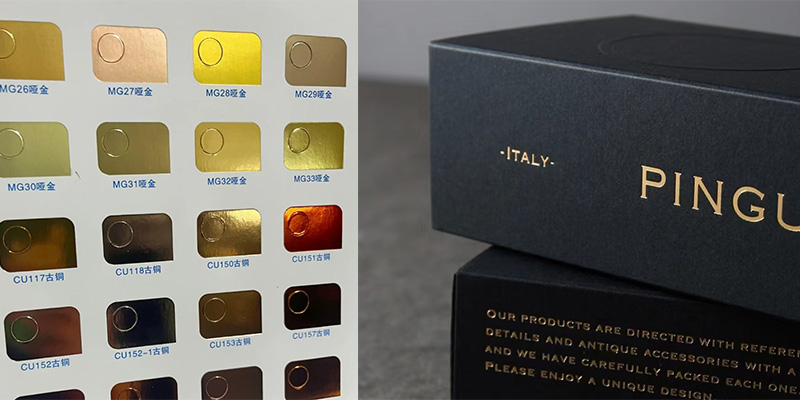
7. Foil Stamping
Foil Stamping Process and Materials
Foil stamping is a traditional printing and decoration process. It forms patterns or texts with a metallic luster on paper or other substrates by applying metal foil, enhancing the aesthetics and luxury of printed products.
Foil Stamping Process:
- Prepare the Foil Stamping Plate:
Make the foil stamping plate by carving or chemical etching based on the designed patterns.
- Place the Foil:
Put the foil on the substrate and align it with the patterns.
- Foil Stamping:
Apply temperature and pressure through the foil stamping machine to make the foil bond with the substrate.
- Cooling and Stripping:
After the foil stamping is completed, cool it down and peel off the excess foil to finish the stamping process.
Foil Stamping Materials:
- Foil:
It usually consists of multiple layers of materials, including a base material (such as PE), a release coating, a color coating, a metal coating (such as aluminum plating), and an adhesive coating.
- Foil Stamping Machine:
It includes heating and pressure devices used to transfer the foil onto the substrate.
- Substrate:
It can be paper, plastic, leather, fabric, etc. Different substrates may require different foil stamping conditions.
Foil Stamping Effects:
- Metallic Luster: Foil stamping provides a unique metallic luster, making printed products look high-end and elegant.
- Three-Dimensional Effect: The patterns after foil stamping have a certain three-dimensional effect, enhancing the visual impact of printed products.
- Anti-counterfeiting Function: Special foil stamping techniques can be used for anti-counterfeiting labels and valuable securities to improve the security of products.
Foil Stamping Effects and Applications
Foil stamping technology has been widely used in many fields due to its unique decorative effects.
Application Fields:
- Luxury Packaging: For example, in the packaging of high-end cosmetics, alcoholic beverages, tobacco and other products, it can enhance the market positioning of products.
- Book Covers: Foil stamping is used on the covers of hardcover books and special edition books to increase their collection value.
- Business Printing Products: Such as business cards, invitations, certificates, etc., it can enhance the formality and professionalism of printed products.
- Garment Industry: Foil stamping is used on garment labels and decorations to increase the fashion sense of clothing.
- Electronic Products: For example, on mobile phone cases and computer casings, it can enhance the aesthetics and brand recognition of products.
Market Trends:
- Growth in Personalization Demand:
As consumers' demand for personalized products increases, the application of foil stamping technology in personalized printed products will continue to grow.
- Technological Progress:
The foil stamping technology is constantly improving. For example, the development of cold foil stamping technology makes the foil stamping process more environmentally friendly and efficient.
- Increased Environmental Awareness:
Environmentally friendly foil stamping materials and processes will be more popular, reducing the impact on the environment.
- Online Printing Services:
The rise of online printing platforms makes foil stamping services more convenient and accessible.
Foil stamping technology plays an important role in the modern printing industry with its unique metallic luster and high-end decorative effects. With the progress of technology and the development of the market, the application fields of foil stamping will be further expanded.
Summary
Designers need to understand printing processes because it is an important part to ensure that design works are perfectly presented from digital drafts to actual finished products. Each printing process has its own unique advantages and limitations. Understanding these differences can help designers achieve their design intentions more effectively. By knowing these differences, designers can better choose the appropriate process according to the project requirements to ensure that the design effects are presented as expected.
Meanwhile, different printing processes have different requirements for materials, colors, resolutions, etc. Only by understanding these details can designers make corresponding adjustments in the design stage to avoid problems such as color deviation, blurring or distortion in printing. For example, screen printing is suitable for thick ink effects and can present a unique tactile and visual texture on T-shirts and packaging, while gravure printing is more suitable for high-quality images and gradient effects.
In addition, mastering printing processes can also help designers control costs and optimize time. Designers who are familiar with special processes such as foil stamping and UV printing can choose the appropriate process to achieve a more impactful visual effect within the budget. Therefore, understanding printing processes not only enhances the professional abilities of designers but also ensures the perfect implementation of design works from creativity to finished products.